This interview previously appeared in Green Energy Times.
Interview with Steve Sisler, Founder and CEO
Interview by Michael J. Daley
Steve Sisler began his company in 1983 after earning his degree in industrial economics from Union College in Schenectady, NY. For the past 40 years, he and his crews and teams of subcontractors have been building high quality custom homes and remodels in the northcentral Vermont ski country where there is a vigorous market for second homes. Sisler employs 30 people, including his son, Luke. We will learn what his other son is up to in the following interview.
How do the elements of your business divide out?
It fluctuates year to year, naturally, but currently we are abou10% energy division, 8% custom woodworking, 7% small projects/handyman, 45% new homes and 30% remodels.
Your clients are primarily financially successful people. The projects showcased in your portfolio are stunning houses straight out of the pages of House Beautiful and Fine Homebuilding. Do you find that clientele interested in energy efficiency?
It’s really only in the last few years that I’m seeing a change in people’s consciousness. Almost everyone is interested in heat pumps whether air source or geothermal. We have not built a recent project with a fossil fueled primary heating system.
As for energy efficiency, you have to ask where are the savings? The answer is the more you spend up front on good design, quality materials and workmanship and a tight envelope then the operational savings are enormous. That also means simple things like choosing materials that don’t need to be repainted every two years.
But it’s not a matter of throwing R100 insulation everywhere like some people think. Perhaps it’s my industrial economics background,
but I’m interested in the optimal balance between cost and results. My son, Nick, and I collaborated on the research. He’s head of
engineering at Ekotrope, a company that evaluates energy efficient design. We found that R55 for ceilings and R33 for walls is the sweet
spot for us.
Are your clients making design choices that reflect the increasing severity of climate disruptions?
Definitely we do more planning with extreme weather events in mind. There’s more thought given to ancillary systems like power walls or
generators. 100% of our projects use those now. Water management is always an active discussion with more attention to guttering and
basement protection.
Mike D’Muhala, head of your energy division, considers a tight envelope the single most important element in home comfort and efficiency. Do you agree?
Yes, I’m very proud of our focus on a tight envelope. In the past ten years we have not had an ACH50 blower door test rating over one air change per hour, and often less for our new homes. The national standard is three. We achieve our results by testing three times during construction. First when all the mechanicals are in but before the interior paneling, so we can more easily fix any issues that show up. Second after the drywall, appliances and fireplaces are in. Third at the finish, so we can give our customers the certificate and bragging rights to their friends.
You’ve said “Professional relationships are about good communication without stepping on anyone’s toes.” You take pride in building harmonious relationships between clients, architects, designers and the many other subcontractors critical to a project’s success. Is that a talent that came naturally to you, or did that skill evolve over time?
I think it’s always evolving. I went from a college with 2,300 students to Stowe with 3,000 people. So, I learned quickly how vital a good reputation is for working with people. I’m trying to pass along that skill to my sons, giving them details about how to work with people to ensure they will want to keep working with you into the future.
What is your own home like?
When my wife, Sharon, and I came to the area, we found a burnt out 1805 farmhouse in Waterbury Center. The house was derelict, but I saw the potential for salvage and in the property. The trim was American chestnut, now extinct. I saved all that. I was reclaiming materials before that became a catchword. We were on a shoestring budget so we actually turned the horse barn into our house. Today, the house is net zero with heat pumps, an electric boiler, and solar powered including charging my EV.
Is there an aspect of the home building process that most gets your motor going?
I really enjoy relationship building with a new customer and leveraging that trust to give suggestions for finish details that look great but don’t cost a lot. My grandfather, a depression era fine woodworker himself, used to save and unbend old nails. That’s in my heritage, and I’m occasionally caught off guard by people who haven’t worked in the field with hammer and nail who seem to have the attitude that cost isn’t even a variable. It always is for me, and for my clients, however wealthy. Beauty is doing something really stunning but at a reasonable cost that I and the homeowner can appreciate. That’s what excites me.
Michael J. Daley is a life-long renewable energy educator and advocate, except for a brief time in high school when he though nuclear power was cool. He lives in a tiny off-grid cabin in Westminster, VT with his wife, Jessie Haas.
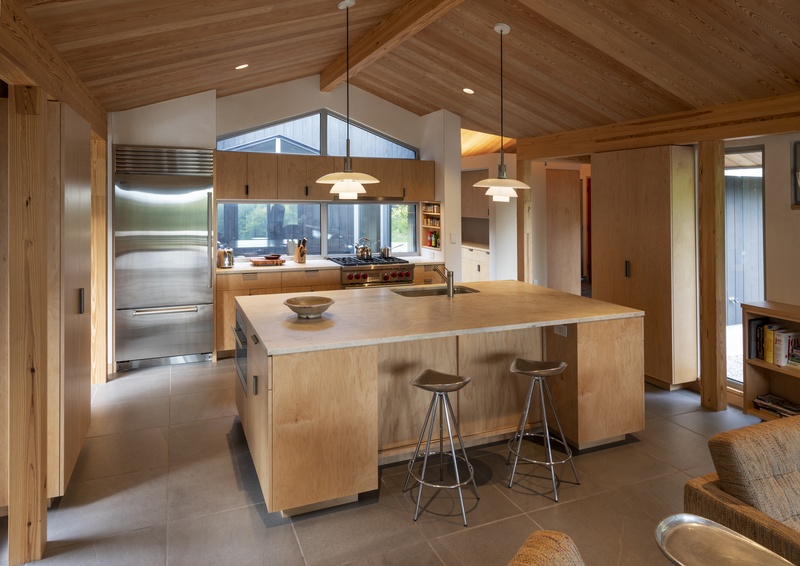
A Sisler Builders’ project showcasing economic use of space with well-crafted details. Sisler custom-made the cabinetry to utilize the available area. The design includes efficient radiant heat and passive and active solar with rooftop solar panels.